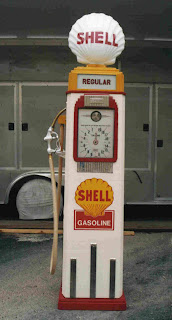
The first gasoline pump was invented and sold by Sylvanus F. Bowser in Fort Wayne, Indiana on September 5, 1885. This pump was not used for automobiles, as they had not been invented yet. It was instead used for some kerosene lamps and stoves. He later improved upon the pump by adding safety measures, and also by adding a hose to directly dispense fuel into automobiles. For a while, the term bowser was used to refer to a vertical gasoline pump. Although the term is not used anymore in the United States, it still is used sometimes in Australia and New Zealand.
Many early gasoline pumps had a calibrated glass cylinder on top. The desired quantity of fuel was pumped up into the cylinder as indicated by the calibration. Then the pumping was stopped and the gasoline was let out into the customers tank by gravity. When metering pumps came into use, a small glass globe with a turbine inside replaced the measuring cylinder but assured the customer that gasoline really was flowing into the tank.
A modern fuel dispenser is logically divided into two main parts — an electronic "head" containing an embedded computer to control the action of the pump, drive the pump's displays, and communicate to an indoor sales system; and secondly, the mechanical section which in a ‘self contained’ unit has an electric motor, pumping unit, meters, pulsers and valves to physically pump and control the fuel flow.
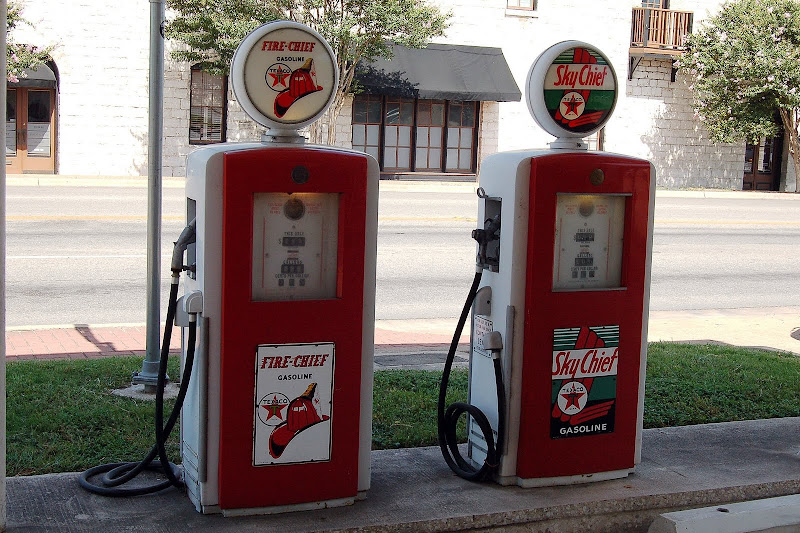
In some cases the actual pump may be sealed and immersed inside the fuel tanks on a site, in which case it is known as a submersible pump. In general submersible solutions in Europe are installed in hotter countries, where suction pumps may have problems overcoming cavitation with warm fuels or when the distance from tank to pump is longer than a suction pump can manage.
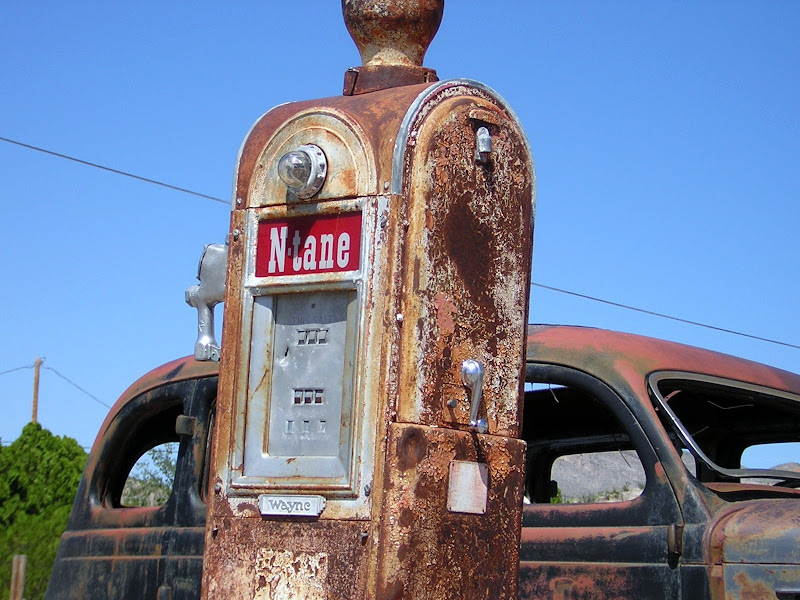
In modern pumps, the major variations are in the number of hoses or grades they can dispense, the physical shape, and the addition of extra devices such as pay at the pump devices and attendant "tag" readers.
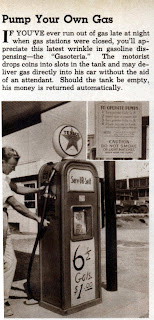
Nozzles are attached to the pump via flexible hoses, allowing them to be placed into the vehicle's filling inlet. The hoses are made very tough to survive hardships such as being driven over, and are often attached using heavy duty spring or coil arrangements to provide additional strength.
The nozzles are usually color coded to indicate which grade of fuel they dispense, however the color coding differs between countries or even customers. For example, a black handle is used in the UK to warn people that the fuel dispensed is diesel. In the United States, diesel fuel pumps commonly use green hoses and green slipcovers over the nozzle.
In some countries, pumps are able to mix two grades of fuel together before dispensing; this is referred to as blending or mixing. Typical usages are in a "mix" pump to add oil to petrol for two-stroke motorcycles, to produce an intermediate octane rating from separate high and low octane fuels, or to blend hydrogen and compressed natural gas (HCNG).
.
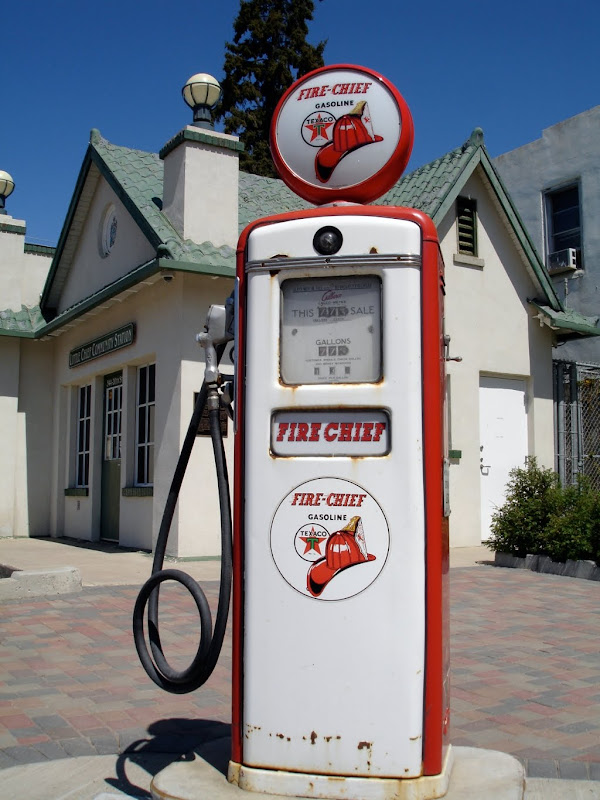
One of the most important functions for the pump is to accurately measure the amount of fuel pumped. Flow measurement is typically done by a turbine in the fuel flow. In older gas pumps, the turbine is physically coupled to reeled meters (moving wheels with numbers on the side), while newer pumps turn the turbine's movement into electrical pulses using a rotary encoder.
Most modern pumps have an auto cut-off feature that stops the flow of fuel once the tank is full. This is done by having a second tube, the sensing tube, that runs from just inside the mouth of the nozzle up to a Venturi pump in the pump handle. While the tank is being filled, air displaced from the tank is drawn up this tube. Once the fuel level reaches the mouth of the sensing tube, air is no longer drawn up the sensing line. A mechanical valve in the pump handle detects this change of pressure and closes, preventing the flow of fuel.
.
No comments:
Post a Comment